Introduction
Establishing a consistent and realistic schedule is a significant challenge in the highly regionalized and variable construction industry. Construction executives overseeing projects across different regions, such as U.S., Europe, and Asia data centers, need a reliable method to benchmark project timelines.
Benchmarking in construction is the process of comparing a project’s performance, processes, or standards against industry best practices, standards, or the performance of similar projects. It allows you to understand where you stand compared to your expectations and highlights areas for improvement. This process helps set realistic goals, improve resource allocation, and reduce costs. However, traditional approaches based on estimates and past experiences often need to be revised, leading to inaccuracies, delays, and cost overruns.
Data Center Construction: The Importance of Benchmarking
Data center construction presents unique challenges due to the need for specialized systems like redundant power, rooftop control units, automatic transfer switches, and fire suppression systems. These features are essential for ensuring high operational standards and reliability.
To maintain project success and adhere to stringent timelines, referencing benchmarks in data center construction is critical. Benchmarks provide a reliable framework to keep projects on schedule by aligning construction activities with established standards. For instance, systems like redundant power and climate control must be installed according to precise timelines to avoid disruptions.
Owners can prevent construction delays by utilizing tools like Doxel to track each phase of construction, comparing progress against benchmark data from previous projects. Understanding the time required for each phase is vital, especially since timelines can vary due to regional and environmental factors. Traditional estimates often lead to inaccuracies, resulting in delays and cost overruns. However, leveraging benchmarks based on actual production data reduces these risks, enabling the creation of more realistic and reliable construction schedules.
The Challenges:
Large complex construction projects with accelerated schedules often lack production data due to a combination of factors related to the complexity, variability, and traditional practices within the industry. Here are some key reasons:
1. Project Complexity and Variability
- Unique Project Requirements: Each large construction project is often unique, with different designs, site conditions, materials, and labor forces. This variability makes it difficult to standardize production data across different projects.
- Custom Workflows: Many large projects involve customized workflows and bespoke solutions, which can vary significantly from one project to another. As a result, collecting and comparing production data becomes more challenging.
2. Fragmented Industry Practices
- Multiple Subcontractors: Large projects typically involve numerous subcontractors, each responsible for different aspects of the work. These subcontractors may have their own methods of tracking progress, which may not be standardized or shared with the general contractor.
- Lack of Centralized Data Management: Often, there is no centralized system for collecting and managing production data across all subcontractors and phases of the project. This fragmentation leads to gaps in data collection and reporting.
3. Traditional Work Methods
- Reliance on Experience and Estimations: The construction industry has traditionally relied on the experience and judgment of skilled professionals rather than data-driven approaches. This reliance on “gut feeling” and historical estimates rather than empirical data can result in a lack of detailed production metrics.
- Paper-Based Processes: Despite advancements in technology, many construction projects still rely on paper-based processes for documentation and reporting. This makes it difficult to collect, aggregate, and analyze production data efficiently.
4. Inconsistent Data Collection Practices
- Varied Data Collection Methods: Different teams within a project may use different tools and methods for data collection, leading to inconsistencies. This lack of standardization can make it challenging to compile accurate and meaningful production data.
- Manual Data Entry Errors: When data collection is done manually, it is prone to errors, omissions, and inconsistencies. These errors can render the data unreliable for creating benchmarks or analyzing production rates.
5. Cost and Time Constraints
- Data Collection Costs: Gathering comprehensive production data can be costly, requiring investment in technology, training, and additional personnel. On tight budgets, these costs may be deemed unnecessary or impractical.
- Time-Consuming Process: Collecting and analyzing detailed production data can be time-consuming, particularly on fast-paced projects where schedules are tight. The perceived burden of data management can lead to it being deprioritized.
6. Technological Adoption Barriers
- Resistance to Change: The construction industry has been slow to adopt new technologies that facilitate data collection and management. Resistance to change and the perceived complexity of new systems can hinder the adoption of tools that could help gather production data.
- Lack of Integration: Even when technology is adopted, it may not be fully integrated across all aspects of the project. Disconnected systems can result in siloed data that isn’t easily accessible or usable for broader analysis.
7. Short-Term Focus
- Focus on Immediate Outcomes: The pressure to deliver projects on time and within budget often leads to a short-term focus on immediate tasks rather than long-term data collection and analysis. As a result, production data is not prioritized as a key project deliverable.
The lack of production data in large construction projects is a multifaceted issue rooted in the complexity of projects, traditional industry practices, fragmented data management, and the challenges of technological adoption. Addressing these barriers requires a shift towards more standardized, data-driven approaches and greater investment in tools and processes that facilitate the collection, analysis, and use of production data across the construction industry.
Production Rates Before Doxel:
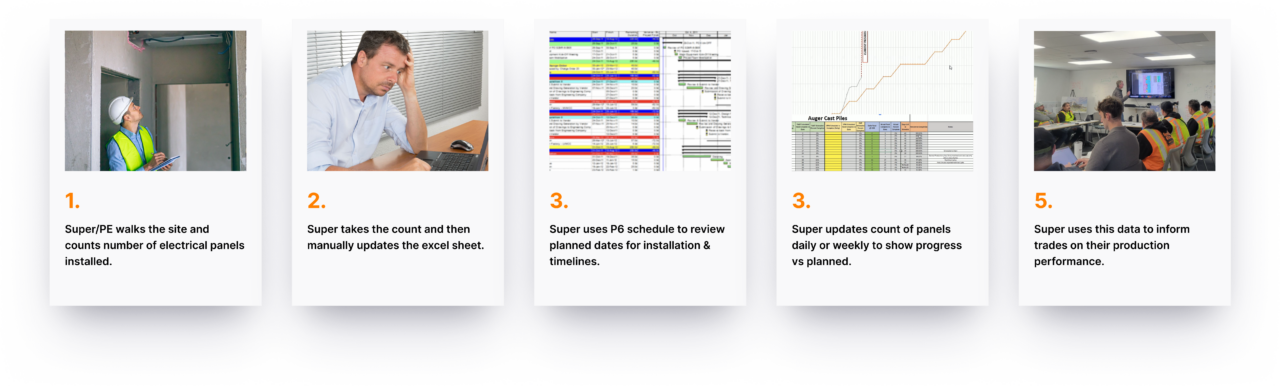
Benchmarking Without Actual Production Data
In major construction projects, the ability to plan, execute, and deliver on time and within budget is critical. However, one of the significant challenges many projects face is the lack of access to reliable production rates and the difficulty in creating accurate benchmarks. These data points are essential for informed decision-making, resource allocation, and performance tracking. Without them, project managers and teams often operate in the dark, leading to inefficiencies, cost overruns, and increased risk. The key challenges that arise when production rates are not readily available and benchmarks are insufficient, highlight the importance of overcoming these issues for project success. They include:
1. Inaccurate Project Estimations
- Lack of Baseline Data: Without access to production rates, project managers struggle to establish accurate baseline data for labor, material, and equipment usage. This leads to inaccurate cost estimates and timelines, resulting in budget overruns and delays.
- Unreliable Scheduling: Estimations based on assumptions rather than historical data can result in unrealistic schedules, which may cause disruptions and conflicts across different project phases.
2. Inefficient Resource Allocation
- Over or Under-Allocation: Without reliable benchmarks, allocating resources such as labor, machinery, and materials becomes a guessing game. Over-allocation leads to unnecessary costs, while under-allocation can cause delays and productivity losses.
- Difficulty in Scaling: Large projects often require the ability to scale operations quickly. The absence of production rates hampers the ability to predict resource needs accurately, leading to inefficiencies and bottlenecks.
3. Poor Performance Tracking
- Lack of Real-Time Data: Without production rates, it is challenging to track performance against benchmarks in real time. This makes it difficult to identify issues early and take corrective action before they escalate.
- Difficulty in Benchmarking: Creating benchmarks requires historical data to compare current performance. Without this data, teams may rely on industry averages that do not accurately reflect the specific conditions of the project, leading to skewed performance evaluations.
4. Challenges in Continuous Improvement
- Limited Feedback Loop: Without detailed production rates, it is difficult to establish a feedback loop that informs continuous improvement. Teams lack the necessary data to analyze what worked well and what didn’t, hampering efforts to refine processes and increase efficiency over time.
- Inconsistent Best Practices: Without benchmarks, it is challenging to identify and replicate best practices across different projects or phases. This inconsistency can lead to varying levels of quality and efficiency, even within the same organization.
5. Increased Risk and Uncertainty
- Higher Risk of Disputes: In the absence of clear benchmarks, disagreements over performance, costs, and timelines are more likely to arise, leading to potential disputes between contractors, subcontractors, and clients.
- Greater Project Uncertainty: The lack of reliable data increases the overall uncertainty of the project, making it harder to manage risks effectively. This uncertainty can impact stakeholder confidence and potentially lead to financial and reputational damage.
Not having access to production rates and benchmarks in major construction projects can lead to a range of challenges, from inaccurate estimations to poor performance tracking and increased risk. Addressing these issues requires a concerted effort to gather, analyze, and utilize data effectively to create reliable benchmarks and optimize project outcomes.
Doxel is an automated progress tracking solution that provides real-time, objective data on construction performance. Unlike traditional methods that rely on manual tracking and subjective reporting, Doxel uses AI and computer vision to deliver frequent, precise, actionable insights. Doxel speeds up construction by automating progress reporting which surfaces hidden issues early, prevents rework, and enhancing collaboration with visual data.
Production Rates After Doxel:
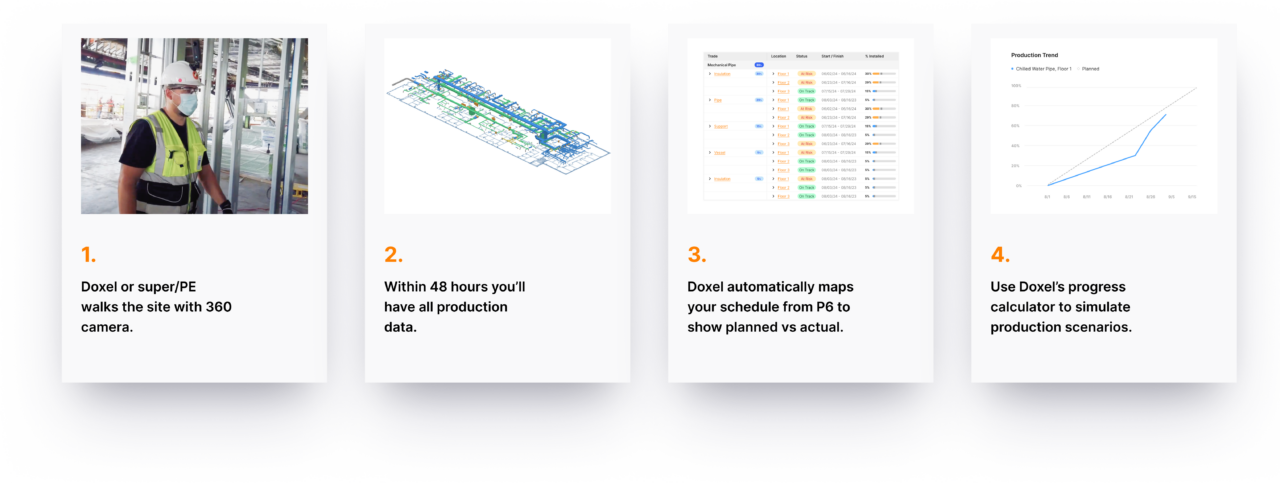
Accurate Benchmarking: The Solution
Doxel’s automated progress tracking leverages images from 360 degree cameras for reality capture by converting images into construction elements. This technology provides precise data on production rates, such as linear feet of conduit installed per week across multiple projects. By comparing this data across different trades, sites, and contractors, Doxel enables teams to create more realistic schedules based on actual performance metrics.
Controlling Project Schedules with Benchmark Data
Owner’s reps, sometimes considered the Director of Construction, are responsible for fostering collaboration between stakeholders to bring data centers and large projects in on schedule and under budget. Consider a scenario where an owner has built multiple data centers using Doxel and has significant benchmark data on productivity rates for each stage in construction. This collaboration can provide enormous benefits when analyzing bids from the GC. Where project schedules are overly aggressive, project owners can challenge GCs on their ability to commit to accelerated schedules, fostering a sense of alignment. With Doxel’s historical production rate data, the GC can confidently assess the feasibility of the proposed schedule. The added transparency between the owner and GC, facilitated by Doxel, helps deliver projects on schedule using historical benchmark data.
Managing Production Rates in Doxel
Benchmarking: Use Historical Data to Set Realistic Schedules
- Doxel allows construction teams to benchmark using historical data, ensuring that schedules are based on actual performance rather than estimates. This approach provides a solid foundation for setting realistic project timelines.
Risk Reduction: Avoid Overcommitting and Mitigate the Risk of Delays
- Avoid Overcommitting and Mitigate Risk: By relying on accurate production data, teams can prevent overcommitting, reducing the risk of delays and cost overruns to keep projects on track.
- Deliver Accelerated Schedules with Certainty: Leveraging precise data enables teams to confidently meet the demand for faster project completion, ensuring speed without compromising quality or increasing risk.
Informed Decision-Making: Make Data-Driven Decisions That Clients Trust
- With precise production data at their fingertips, construction teams can make informed decisions that clients trust. This transparency builds confidence and strengthens client relationships.
Enhanced Reputation: Deliver Projects on Time and Within Budget
- Delivering projects on time and within budget boosts a construction firm’s reputation and secures future business. By leveraging Doxel, teams can consistently meet or exceed client expectations.
Conclusion
In the construction industry, informed scheduling decisions are crucial for project success. Doxel’s production rate data provides insights to optimize schedules, reduce risks, and ensure successful project delivery. By leveraging this data, construction teams can confidently commit to achievable timelines and deliver exceptional results.
Ready to optimize your project schedules with Doxel’s production rate data? Contact us today for a demo and discover how Doxel can help your team achieve faster schedules with confidence and reduced risk.
By incorporating these insights and leveraging cutting-edge tools like Doxel, construction teams can navigate the complexities of project scheduling with greater certainty and efficiency.