In his February 5, 2023 opinion piece in the New York Times, Ezra Klein rings the alarm that the $1.6 trillion U.S. construction industry has not shared the productivity gains of other industries. He cites Goolsbee and Syverson’s paper “The Strange and Awful Path of Productivity in the US Construction Sector,” which explains that construction productivity has decreased since 1950 while manufacturing productivity, for example, has increased ninefold. I appreciate Mr. Klein’s alarm as well as his humility in admitting he has no idea how we get construction productivity rising again. Two decades into a career focused on bringing productivity gains to construction, I do have an idea.
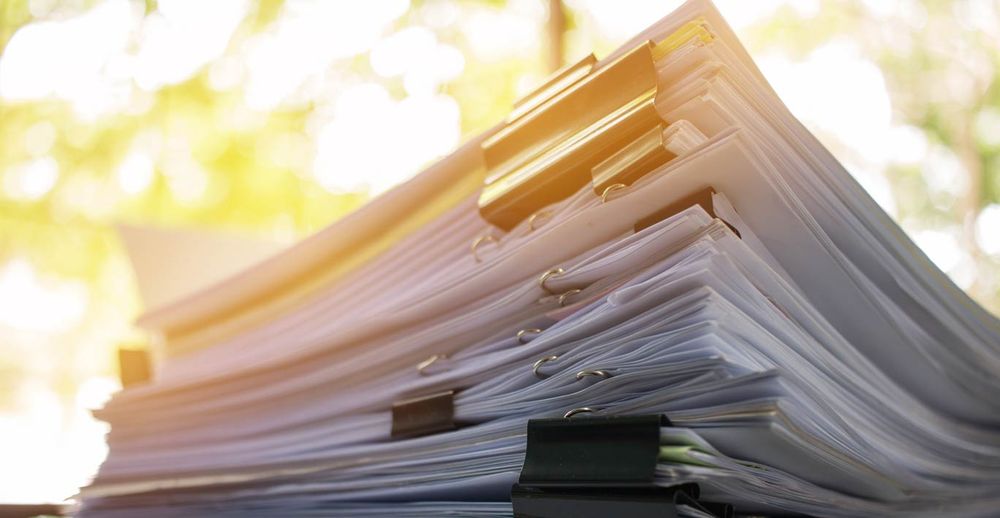
But before I get to my idea, let’s consider Mr. Klein’s prime culprit – regulatory “paperwork, and paperwork, and more paperwork.” No doubt regulation impacts construction productivity; regulation impacts most industries. While Syverson’s paper does not provide data connecting productivity declines to increased regulation, it does note that the construction industry invested 46 percent less in R&D and software purchases compared to the broader economy in 2020. And, a separate paper by Syverson, “The Slowdown in Manufacturing Productivity Growth,” (my fellow construction colleagues will take solace in knowing we are not alone in facing Syverson’s economic scrutiny) explains that information technologies (IT) were the main driver for productivity gains in manufacturing from 1994 to 2005.
Why did IT so dramatically impact manufacturing, but not construction? In both construction and manufacturing, IT can improve productivity once information about the real world is transformed into data. Consider an assembly line producing widgets. The assembly line has sensors that send data to machines to respond in real time and to plant managers who learn of bottlenecks and continuously improve the assembly line. This investment in sensors produces the data that powers IT and drives productivity increases.
Applying IT to construction is not so easy. While a factory produces millions of widgets, a construction project is the assembly of millions of different components to produce only a single facility. A single sensor cannot automatically monitor the installation of thousands of square feet of walls or linear feet of ductwork. And that limitation means that IT is starved of data that would help construction workers and managers gain insights to continuously improve their processes. Thus, until recently, investment in IT has been limited to the design phase and certain aspects of construction administration. Yet, labor is the greatest cost on any project in the U.S. And, IT has had virtually no impact on the productivity of that skilled craftworker laying a brick or welding a beam to a column.
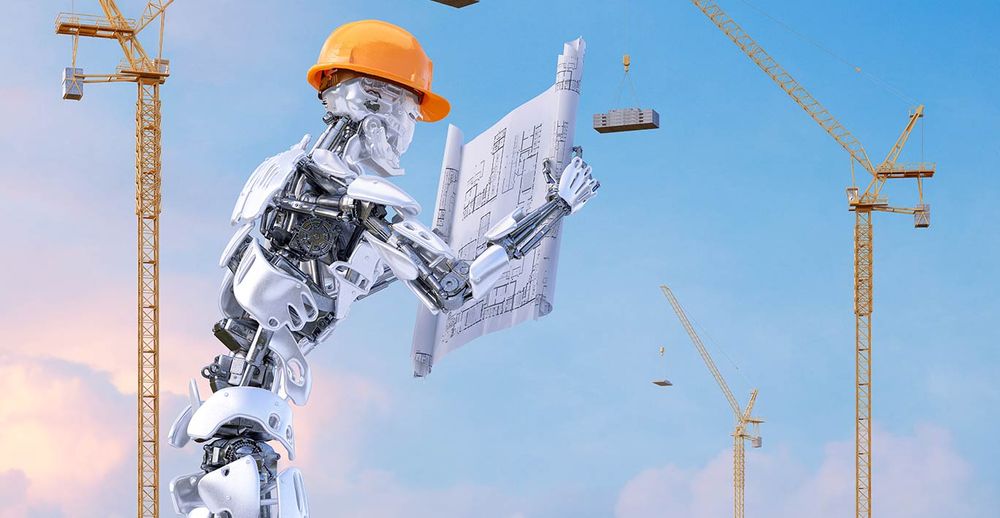
But, that reality is changing. With artificial intelligence (AI) and computer vision, leading builders are transforming 360 video into near real-time measurements of construction processes. This near real-time reality capture of the construction site acts like sensors in a factory, feeding IT with data that empowers project teams to increase productivity. For example, a construction superintendent constructing a retirement community recently used this automated progress tracking technology to identify that a certain duct installation activity was not yet complete on the 3rd floor. Ceilings were set to be installed the next day. Without this insight from technology, the unfinished ductwork would have been covered up by the ceiling trade partner. And, when they later discovered the oversight, they would have had to rip open the ceiling. That rework would have put a big dent in their productivity. Instead, the AI-powered IT indicated the ductwork was not 100% complete. Augmented with this information, the superintendent applied his expertise in coordinating trades to get the ducts installed right away to avoid the rework. And, the general contractor and retirement community owner no longer had to explain to residents why they were going to be moving in two weeks late.
This technology is new; we only began building it in 2015. But we’re seeing results. At Doxel, we’ve created automated progress tracking for construction that reduces time spent manually tracking progress by 95%. This automation creates data that is now fueling productivity gains from IT just like in manufacturing. And, it gets data to decision makers 5x – 10x faster, which gives 5x – 10x the opportunities to unlock the full potential of construction teams to accelerate schedules and deliver projects under budget. We’re not alone in augmenting construction team expertise with AI; companies such as Procore, Autodesk, Oracle, Dusty, Rhumbix and dozens of others have built technology that makes construction easier for millions of workers every day. And, forward looking facility owners are hungry to adopt solutions that reduce their risk and make the job easier for superintendents and trade partners, because they know the investment will translate to projects that are on time and on budget.
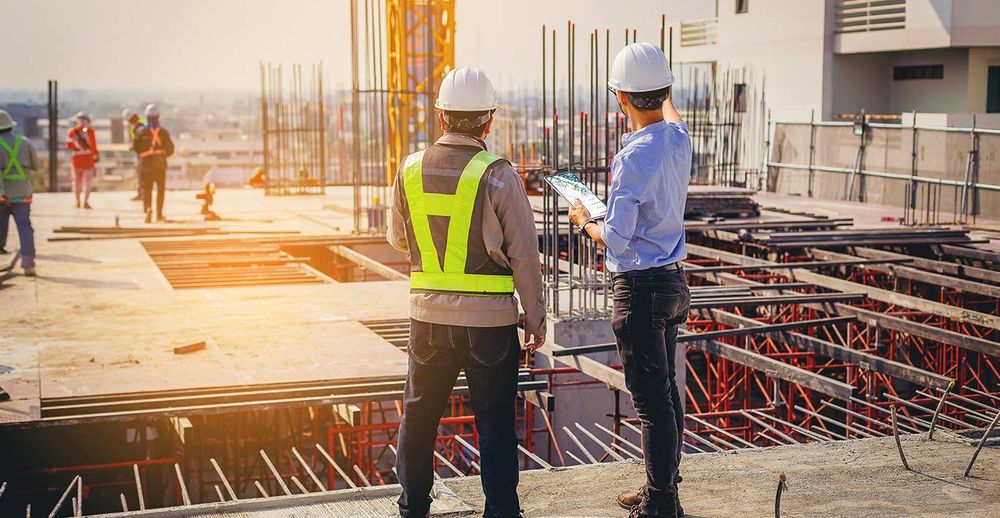
Of course, an industry’s health depends on more than a single metric. Construction provides nearly 11 million jobs in the U.S., including many high paying roles that do not require a college degree. They are rewarding jobs that contribute to society. But, the work is not easy. It frequently requires complex problem solving or complex physical skills. These are great jobs, partially because they can’t be easily automated to increase productivity. Still, productivity is an important metric not just for economists, but because it tends to correlate with the industry’s per capita income. According to Syverson, construction pay could be 10% higher if the industry’s productivity gains tracked the economy as a whole. Society needs construction to be easier, too. As we face challenges supplying healthcare, delivering energy, and investing in infrastructure, construction will either be a bottleneck to change or it will be a catalyst to change. AI augments the experience and skills of construction teams, so they have better data and tools and owners have the confidence to invest in projects that solve society’s 21st Century challenges.
Written by Reid Senescu, California Licensed Professional Engineer and PhD in Civil and Environmental Engineering from Stanford University. He is the Vice President of Product at Doxel.ai in Menlo Park, California. His research focused on how technology can improve construction team collaboration. At Doxel.ai, his products use computer vision to help teams collaborate and deliver projects on time and on budget.